کوره القایی یک کوره الکتریکی است که در آن گرما توسط گرمایش القایی تأمین می گردد. [ ۱] [ ۲] [ ۳] ظرفیت کوره های القایی از کمتر از یک کیلوگرم تا صد تن متغیر بوده و برای ذوب آهن و فولاد، مس، آلومینیوم و فلزات گرانبها کاربرد دارد.
مزیت اصلی کوره القایی فرایند ذوب تمیز، کم مصرف و کنترل دقیق متالورژی ماده مذاب[ ۴] در مقایسه با بیشتر روش های ذوب فلز است. امروزه بیشتر کارخانه های ریخته گری مدرن از این نوع کوره ها استفاده می کنند و کارخانه های ریخته گری دیگر نیز به دلیل آلودگی بالای کوره های بلند، در حال جایگزینی آن ها با کوره های القایی هستند. [ ۵]
از آنجایی که از قوس الکتریکی و احتراق استفاده نمی شود، دمای مواد بالاتر از حد لازم برای ذوب شدن آن نیست که کمک می کند عناصر آلیاژی ارزشمند از دست نروند. [ ۶]
یک اشکال عمده در استفاده از کوره های القایی، نداشتن توان تصفیه است. مواد شارژ باید عاری از محصولات اکسیداسیون بوده و دارای ترکیب شناخته شده باشند و مقداری از عناصر آلیاژی ممکن است به دلیل اکسیدشدن ازبین بروند ( و باید دوباره به مذاب اضافه شوند ) .
در گذشته فرکانس کاری کوره های القایی برابر ۶۰ هرتز ( فرکانس برق شهری آمریکا ) بوده، اما با پیشرفت های بزرگ ایجاد شده در صنعت الکترونیک، روش های تبدیل فرکانس حالت - جامد، امروزه کوره هایی بسیار بهینه با فرکانس هایی در محدوده ۷۰ تا ۱۰۰۰۰ هرتز نیز قابل تولید است. [ ۴]
نحوه کارکرد پایه ای کوره القایی به این صورت است که ولتاژ بالای موجود در کویل اصلی، باعث القای ولتاژ پایین ولی جریان بالایی در فلز قراضه ها می شود، که به عنوان کویل ثانویه عمل می کند. به دلیل مقاومت الکتریکی موجود در فلز، این انرژی الکتریکی تبدیل به گرما شده و باعث ذوب شدن آن می شود. زمانی که فلز کاملاً ذوب شود، میدان مغناطیسی موجود باعث ایجاد یک خاصیت همزنی می شود. توان و فرکانس اعمالی میزان این عمل همزنی را تعیین می کنند. [ ۴]
دو دسته بندی کلی برای کوره های القایی وجود دارد: کوره القایی بدون هسته ( Coreless Type ) و کوره القایی کانالی ( Channel Type ) . در کوره القایی بدون هسته یا کورلس، بوته دارای آستر نسوز، به صورت کامل توسط یک کویل مسی خنک شونده توسط آب احاطه شده است، در حالیکه در کوره القایی نوع کانالی کویل فقط دور زائده ای از بوته پیچیده شده است که به آن القاگر می گویند. از کوره های کورلس بیشتر برای ذوب و سوپرهیت کردن استفاده شده و از کوره های کانالی بیشتر برای سوپرهیت کردن، دوپلکس کردن و نگهداری مذاب استفاده می شود. [ ۴]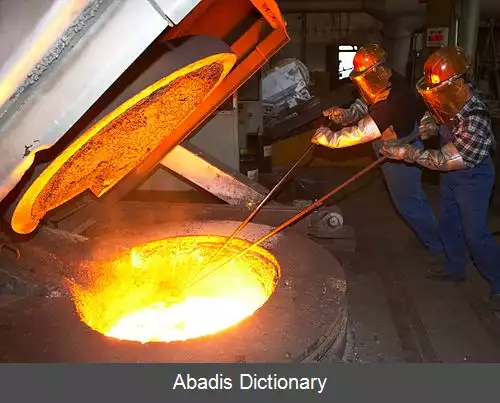
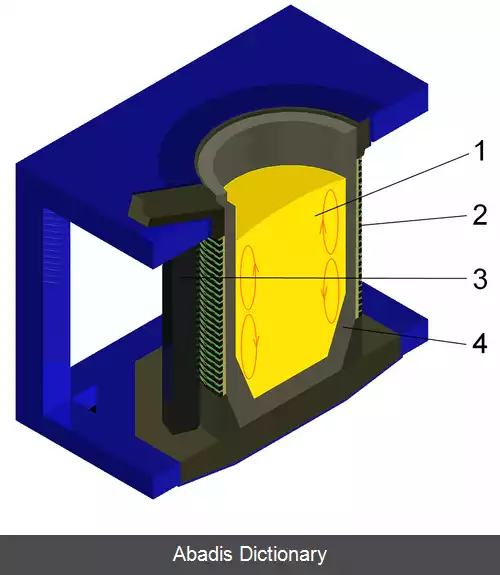
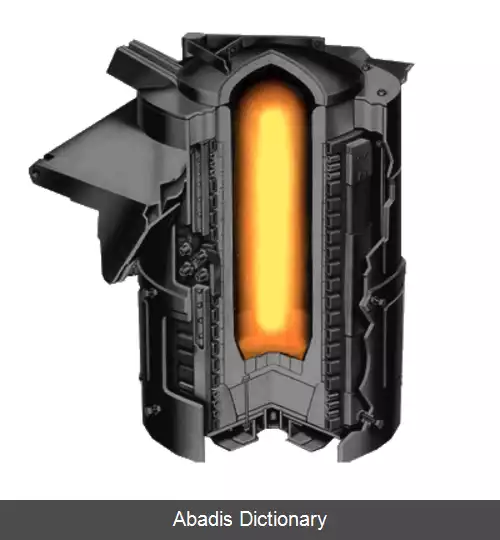
این نوشته برگرفته از سایت ویکی پدیا می باشد، اگر نادرست یا توهین آمیز است، لطفا گزارش دهید: گزارش تخلفمزیت اصلی کوره القایی فرایند ذوب تمیز، کم مصرف و کنترل دقیق متالورژی ماده مذاب[ ۴] در مقایسه با بیشتر روش های ذوب فلز است. امروزه بیشتر کارخانه های ریخته گری مدرن از این نوع کوره ها استفاده می کنند و کارخانه های ریخته گری دیگر نیز به دلیل آلودگی بالای کوره های بلند، در حال جایگزینی آن ها با کوره های القایی هستند. [ ۵]
از آنجایی که از قوس الکتریکی و احتراق استفاده نمی شود، دمای مواد بالاتر از حد لازم برای ذوب شدن آن نیست که کمک می کند عناصر آلیاژی ارزشمند از دست نروند. [ ۶]
یک اشکال عمده در استفاده از کوره های القایی، نداشتن توان تصفیه است. مواد شارژ باید عاری از محصولات اکسیداسیون بوده و دارای ترکیب شناخته شده باشند و مقداری از عناصر آلیاژی ممکن است به دلیل اکسیدشدن ازبین بروند ( و باید دوباره به مذاب اضافه شوند ) .
در گذشته فرکانس کاری کوره های القایی برابر ۶۰ هرتز ( فرکانس برق شهری آمریکا ) بوده، اما با پیشرفت های بزرگ ایجاد شده در صنعت الکترونیک، روش های تبدیل فرکانس حالت - جامد، امروزه کوره هایی بسیار بهینه با فرکانس هایی در محدوده ۷۰ تا ۱۰۰۰۰ هرتز نیز قابل تولید است. [ ۴]
نحوه کارکرد پایه ای کوره القایی به این صورت است که ولتاژ بالای موجود در کویل اصلی، باعث القای ولتاژ پایین ولی جریان بالایی در فلز قراضه ها می شود، که به عنوان کویل ثانویه عمل می کند. به دلیل مقاومت الکتریکی موجود در فلز، این انرژی الکتریکی تبدیل به گرما شده و باعث ذوب شدن آن می شود. زمانی که فلز کاملاً ذوب شود، میدان مغناطیسی موجود باعث ایجاد یک خاصیت همزنی می شود. توان و فرکانس اعمالی میزان این عمل همزنی را تعیین می کنند. [ ۴]
دو دسته بندی کلی برای کوره های القایی وجود دارد: کوره القایی بدون هسته ( Coreless Type ) و کوره القایی کانالی ( Channel Type ) . در کوره القایی بدون هسته یا کورلس، بوته دارای آستر نسوز، به صورت کامل توسط یک کویل مسی خنک شونده توسط آب احاطه شده است، در حالیکه در کوره القایی نوع کانالی کویل فقط دور زائده ای از بوته پیچیده شده است که به آن القاگر می گویند. از کوره های کورلس بیشتر برای ذوب و سوپرهیت کردن استفاده شده و از کوره های کانالی بیشتر برای سوپرهیت کردن، دوپلکس کردن و نگهداری مذاب استفاده می شود. [ ۴]
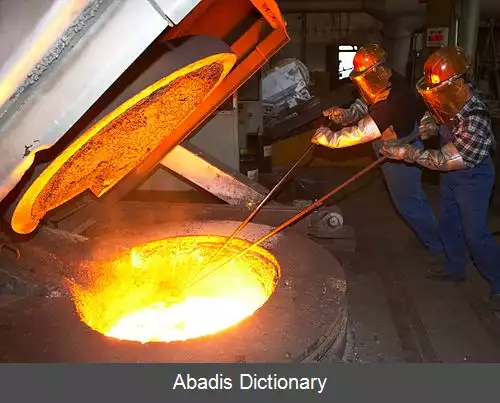
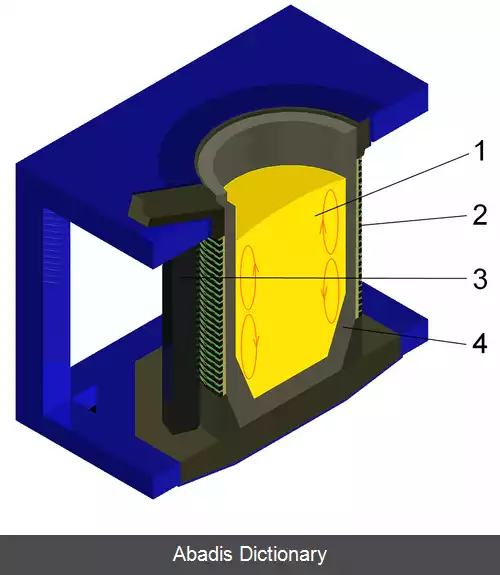
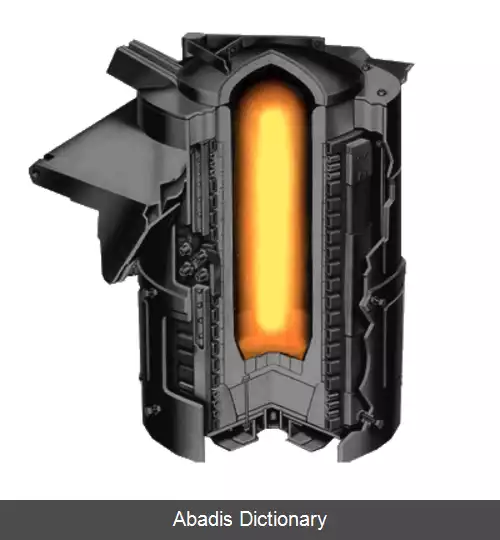
wiki: کوره القائی