پوشش دهی دورانی ( به انگلیسی: Spin coating ) روشی رایج، در علوم و مهندسی، برای نشاندن لایه های نازک و یکنواخت مواد بر روی یک زیرساخت مسطح است. در این روش معمولاً از یک ماده محلول مانند لاک نوری برای لایه زنی استفاده می شود.
این فرآیند به ویژه در صنایع میکروالکترونیک و MEMS برای پوشش قرص سیلیسیم با لاک نوری در فرایند اولیه الگودهی با طرح نگاری نوری کاربرد دارد. هدف از پوششدهی دورانی و با کیفیت بالا، تولید یک لایه لاک نوری یکنواخت و صاف با ضخامت قابل پیش بینی و تکرارپذیر است. تلاش های زیادی برای فهرست کردن پارامترهای ضخامت و یکنواختی این فرآیند در عمل به ویژه برای لاک های نوری استاندارد صورت گرفته است. آنالیز تحلیلی پوشش دهی دورانی بر پایه اصول هیدرودینامیک ( به دلیل پیچیدگی فیزیک و مدل ریاضی ) به صورت جزئی صورت گرفته است. این تحلیل ها دید خوبی در مورد اثرات مطلوب و محدودیت های موجود در فرآیند در اختیار می گذارد.
فرآیند پوششدهی دورانی شامل تزریق لاک نوری بر روی سطح زیرلایه، چرخش سریع برای نازک کردن و پخش ماده بر روی زیرلایه و حرارت دهی و خشکسازی برای حذف حلال اضافی از لاک است. در ابتدا زیر ساخت که معمولاً یک قرص سیلیسیمی است بر روی یک صفحه گردان[ ۱] قرار می گیرد. این صفحه گردان می تواند اندازه هاو طرح های مختلف داشته باشد که معمولاً بسته به اندازه زیر ساخت، مورد استفاده قرار می گیرند. بنابراین صفحات به راحتی قابل تعویض اند. زیر ساخت، از زیر، به کمک خلا مکیده شده و روی صفحه گردان ثابت می شود تا در هنگام چرخش سریع به اطراف پرتاب نشود. برای لایه زنی مقدار معینی از ماده محلول مورد نظر را بر روی مرکز زیرساخت می ریزند. معمولاً از دو روش استاتیک یا دینامیک برای تزریق ماده استفاده می شود. در روش استاتیک، زیرساخت در حال سکون و در روش دینامیک در حال دورانِ آرام ( حدود r p m ۵۰۰ ) است. مقدار این ماده معمولاً بر اساس بزرگی سطح زیر ساخت و غلظت ماده محلول و ارتفاع نهایی لایه مورد نظر از پیش تعیین می گردد. این ماده در اکثر مواقع یک محلول بسپار است که جرم مولی آن تأثیر مستقیم بر روی صخامت لایه دارد ( جزییات بیشتر و ارائه مدل و روابط مربوط در مقاله[ ۲] ) . بر روی دستگاه های پوشش دورانی می توان شتاب، سرعت نهایی دوران و زمان را تعیین کرد. سپس دستگاه با شتاب مورد نظر سرعت گرفته و بعد از دوران با سرعت نهایی در طول زمانی از پیش تعیین شده با شتابی مشخص ترمز می کند. ماده محلول اضافی، بر اثر نیروی گریز از مرکز، از روی سطح زیر ساخت به اطراف پراکنده می شود. به همین دلیل معمولاً این عمل در یک محیط در بسته انجام می گیرد و فضای زیر دستگاه قابل شستشو است و محلی برای جمع آوری ماده محلول اضافی در آن تعبیه شده است. این روش باعث ایجاد یک لایه همگن بر روی بخش وسیعی از سطح زیرساخت می شود. تغییراتی در حدود r p m ۵۰ منجربه اختلافی به اندازه ۱۰٪ در ضخامت لایه خواهد شد. همیشه در کناره های زیر ساخت به علت کشش سطحی بالا بین مولکول های ماده محلول و لبه زیر ساخت ارتفاع لایه افزایش می یابد و معمولاً مناطق حاشیه ای زیر ساخت به همین دلیل مورد استفاده قرار نمی گیرند. بعضی مواقع به دلیل نیاز یه یک لایه صخیم نمی توان از دستگاه پوشش دورانی استفاده کرد و عملیات پوشش دورانی به صورت دستی انجام می شود. برای مثال با ریختن ماده محلول روی قرص زیر ساخت این قرص، توسط دست، چندین بار به آهستگی چرخانده می شود. این کار نه باید خیلی سریع انجام شود تا از ایجاد حباب و توزیع غیر یکنواخت جلوگیری گردد و نه باید آنقدر آرام انجام شود که با تبخیر و خارج شدن ماده حلال نتوان به یک توزیع یکنواخت رسید. در روش دستی معمولاً قرص لایه زده شده برای مدتی روی حرارت ملایم قرار می دهند تا ماده محلول فرصت لازم برای توزیع یکنواخت روی سطح را پیدا کند. این کار باید در یک فضای بسته ( مثلاً زیر یک ظرف شیشه ای آزمایشگاهی ) انجام شود تا از خروج ماده حلال و سفت شدن محلول جلوگیری شود. با این روش لایه هایی تا ارتفاع بالای ۱ میلی متر هم قابل ساخت است. برای پوشش های ضخیم تر از روش های دیگر و همچنین چسباندن لایه های پیش ساخته بهره گرفته می شود. برای سفت و محکم کردن لایه جدید باید به ماده محلول اجازه داد تا حلال از آن خارج شود. برای تسریع این کار زیرساخت را حرارت می دهند[ ۳] .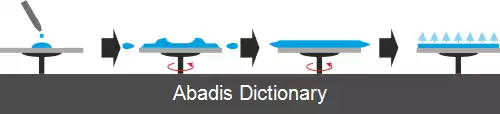
این نوشته برگرفته از سایت ویکی پدیا می باشد، اگر نادرست یا توهین آمیز است، لطفا گزارش دهید: گزارش تخلفاین فرآیند به ویژه در صنایع میکروالکترونیک و MEMS برای پوشش قرص سیلیسیم با لاک نوری در فرایند اولیه الگودهی با طرح نگاری نوری کاربرد دارد. هدف از پوششدهی دورانی و با کیفیت بالا، تولید یک لایه لاک نوری یکنواخت و صاف با ضخامت قابل پیش بینی و تکرارپذیر است. تلاش های زیادی برای فهرست کردن پارامترهای ضخامت و یکنواختی این فرآیند در عمل به ویژه برای لاک های نوری استاندارد صورت گرفته است. آنالیز تحلیلی پوشش دهی دورانی بر پایه اصول هیدرودینامیک ( به دلیل پیچیدگی فیزیک و مدل ریاضی ) به صورت جزئی صورت گرفته است. این تحلیل ها دید خوبی در مورد اثرات مطلوب و محدودیت های موجود در فرآیند در اختیار می گذارد.
فرآیند پوششدهی دورانی شامل تزریق لاک نوری بر روی سطح زیرلایه، چرخش سریع برای نازک کردن و پخش ماده بر روی زیرلایه و حرارت دهی و خشکسازی برای حذف حلال اضافی از لاک است. در ابتدا زیر ساخت که معمولاً یک قرص سیلیسیمی است بر روی یک صفحه گردان[ ۱] قرار می گیرد. این صفحه گردان می تواند اندازه هاو طرح های مختلف داشته باشد که معمولاً بسته به اندازه زیر ساخت، مورد استفاده قرار می گیرند. بنابراین صفحات به راحتی قابل تعویض اند. زیر ساخت، از زیر، به کمک خلا مکیده شده و روی صفحه گردان ثابت می شود تا در هنگام چرخش سریع به اطراف پرتاب نشود. برای لایه زنی مقدار معینی از ماده محلول مورد نظر را بر روی مرکز زیرساخت می ریزند. معمولاً از دو روش استاتیک یا دینامیک برای تزریق ماده استفاده می شود. در روش استاتیک، زیرساخت در حال سکون و در روش دینامیک در حال دورانِ آرام ( حدود r p m ۵۰۰ ) است. مقدار این ماده معمولاً بر اساس بزرگی سطح زیر ساخت و غلظت ماده محلول و ارتفاع نهایی لایه مورد نظر از پیش تعیین می گردد. این ماده در اکثر مواقع یک محلول بسپار است که جرم مولی آن تأثیر مستقیم بر روی صخامت لایه دارد ( جزییات بیشتر و ارائه مدل و روابط مربوط در مقاله[ ۲] ) . بر روی دستگاه های پوشش دورانی می توان شتاب، سرعت نهایی دوران و زمان را تعیین کرد. سپس دستگاه با شتاب مورد نظر سرعت گرفته و بعد از دوران با سرعت نهایی در طول زمانی از پیش تعیین شده با شتابی مشخص ترمز می کند. ماده محلول اضافی، بر اثر نیروی گریز از مرکز، از روی سطح زیر ساخت به اطراف پراکنده می شود. به همین دلیل معمولاً این عمل در یک محیط در بسته انجام می گیرد و فضای زیر دستگاه قابل شستشو است و محلی برای جمع آوری ماده محلول اضافی در آن تعبیه شده است. این روش باعث ایجاد یک لایه همگن بر روی بخش وسیعی از سطح زیرساخت می شود. تغییراتی در حدود r p m ۵۰ منجربه اختلافی به اندازه ۱۰٪ در ضخامت لایه خواهد شد. همیشه در کناره های زیر ساخت به علت کشش سطحی بالا بین مولکول های ماده محلول و لبه زیر ساخت ارتفاع لایه افزایش می یابد و معمولاً مناطق حاشیه ای زیر ساخت به همین دلیل مورد استفاده قرار نمی گیرند. بعضی مواقع به دلیل نیاز یه یک لایه صخیم نمی توان از دستگاه پوشش دورانی استفاده کرد و عملیات پوشش دورانی به صورت دستی انجام می شود. برای مثال با ریختن ماده محلول روی قرص زیر ساخت این قرص، توسط دست، چندین بار به آهستگی چرخانده می شود. این کار نه باید خیلی سریع انجام شود تا از ایجاد حباب و توزیع غیر یکنواخت جلوگیری گردد و نه باید آنقدر آرام انجام شود که با تبخیر و خارج شدن ماده حلال نتوان به یک توزیع یکنواخت رسید. در روش دستی معمولاً قرص لایه زده شده برای مدتی روی حرارت ملایم قرار می دهند تا ماده محلول فرصت لازم برای توزیع یکنواخت روی سطح را پیدا کند. این کار باید در یک فضای بسته ( مثلاً زیر یک ظرف شیشه ای آزمایشگاهی ) انجام شود تا از خروج ماده حلال و سفت شدن محلول جلوگیری شود. با این روش لایه هایی تا ارتفاع بالای ۱ میلی متر هم قابل ساخت است. برای پوشش های ضخیم تر از روش های دیگر و همچنین چسباندن لایه های پیش ساخته بهره گرفته می شود. برای سفت و محکم کردن لایه جدید باید به ماده محلول اجازه داد تا حلال از آن خارج شود. برای تسریع این کار زیرساخت را حرارت می دهند[ ۳] .
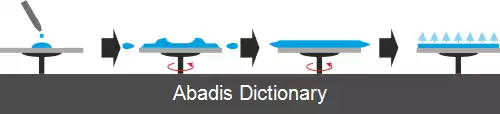
wiki: پوشش دورانی