ریخته گری مداوم (پیوسته). ریخته گری پیوسته، فرایندی است که در آن فلز مذاب برای کاربردهای پسین، به صورت محصولات نیمه ساخته ریخته گری ( همانند شمشال، شمشه و تختال ) تولید می شوند.
در سال ۱۹۵۰؛ برای تولید شمش، فولاد در قالب های ثابت ریخته می شد. از آن پس ریخته گری پیوسته در جهت افزایش کیفیت و کاهش هزینه های تولید پیشرفت های بسیاری کرد. این روش به دلیل داشتن هزینهٔ ذاتی کم و کیفیت بیشتر و همچنین داشتن کنترل در طول فرایند بسیار متداول است.
در واقع؛ شمش های آلومینیوم، برنج، مس، چدن و فولاد با مقطع مربعی، شش گوش و سایر مقطع تولید می شوند. مذاب با نیروی ثقل به داخل کریستالیزاتور هدایت می شود. شمش منجمد شده از مذاب، توسط سیستم کشنده به پایین کشیده می شود.
هنری بسمر، مشهور جهت فرایند بسمر، در سال ۱۸۵۷ حق امتیازی برای ریخته گری بین دو میلهٔ نورد دریافت کرد. اساس این فرایند، امروزه در ریخته گری نوار فولادی استفاده می شود.
فلز مذاب از طریق دهانه داخل کوره ریخته می شود. پس از انجام عملیات مربوط به دهانه؛ همچون ترکیب آلیاژی، گاز زدایی یا رساندن به دمای مناسب، تغذیه به قسمت بالایی دستگاه ریخته گری انتقال می یابد. معمولاً دهانه در محفظهٔ گردانی در بالای دستگاه ریخته گری قرار می گیرد. یکی از منابع تغذیه به صورت on - cast ( درحال تغذیهٔ دستگاه ریخته گری ) و منبع دیگر به حالت off - cast آماده می باشد و هنگامی که منبع تغذیه اولیه خالی شد، جایگزین آن می شود.
فلز داغ از منبع تغذیه توسط لولهٔ دیرگداز وارد حمام ثابتی به نام تاندیش می شود. تاندیش به مخزن فلز اجازه می دهد هنگام تغذیهٔ دستگاه ریخته گری، منبع های تغذیه جایگزین شوند. همچنین به عنوان یک حائل در برابر فلز داغ عمل کرده و به تدریج سیالیت فلز را کاهش می دهد. همین طور موجب تنظیم مقدار تغذیه لازم برای قالب ها و در نهایت تمیزکاری دستگاه می شود.
فلز توسط لولهٔ دیگری از تاندیش تخلیه شده و درون قالب باز مسی ریخته می شود. عمق قالب می تواند بین ۰٫۵ الی ۲ متر ( ۲۰ الی ۷۹ اینچ ) ، بسته به سرعت ریخته گری یا اندازهٔ قسمت، تغییر کند. سپس قالب آب سرد می شود تا فلز به طور مستقیم منجمد شود. این اولین مرحله از روش خنک کاری می باشد. همچنین به صورت عمودی ( و یا در یک راه منحنی عمودی ) نوسان می کند تا مانع چسبیدن فلز به دیواره های قالب شود. یک سیال روان کار ( و یا گاهی به صورت پودری که در برخورد با فلزات یا مایعات ذوب می شود ) اضافه می شود تا مانع چسبیدن و باقی ماندن ذرت در قالب شود – همچون ذرات اکسیدی - که امکان دارد روی فلز باشد و باعث شود روی مذاب جمع شود و یک لایه از ذرات و خاکستر را تشکیل دهد. لوله ای در قسمت پایین تعبیه شده است که مذاب نهفته در زیر لایهٔ ذرات را خارج می کند. به این لوله «نازل ورودی زیرآب» ( SEN ) گفته می شود. در برخی موارد لوله ها بین تاندیش و قالب استفاده نمی شوند. ( ریخته گری ریزش باز ) ؛ در این موارد نازل های قابل سنجش و تنظیم، که در قسمت انتهایی تاندیش قرار دارند، موجب هدایت فلز به داخل قالب می شوند. در برخی از طرح های ریخته گری پیوسته چندین قالب از یک تاندیش تغذیه می شوند.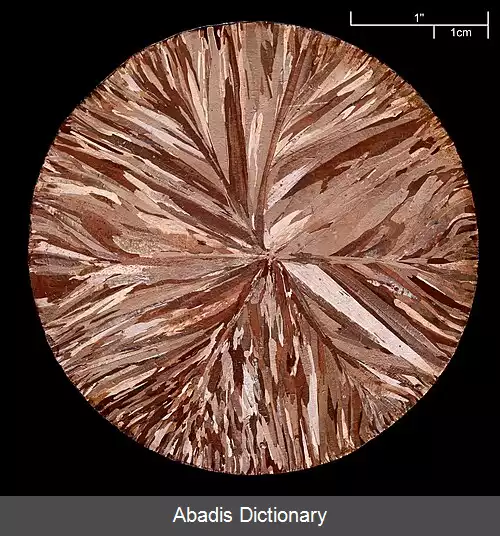
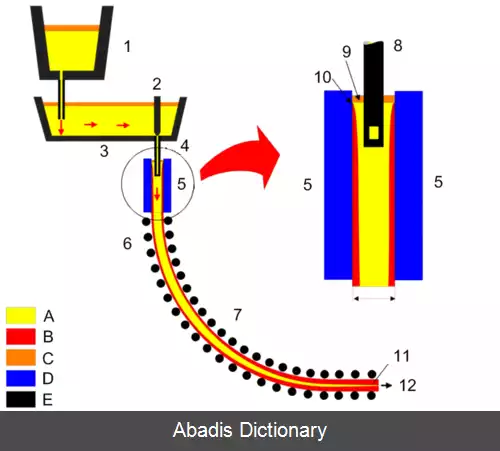
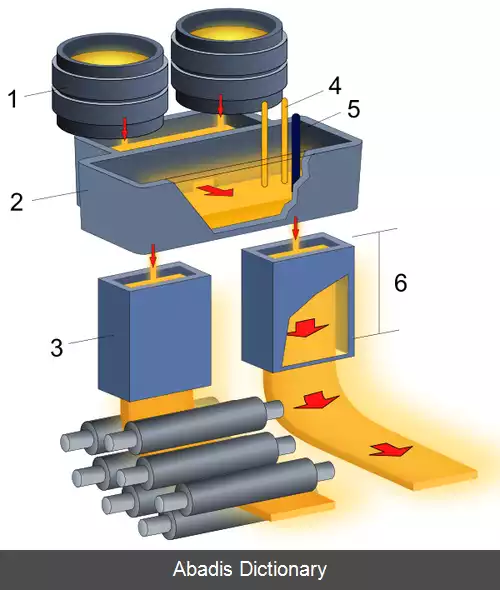
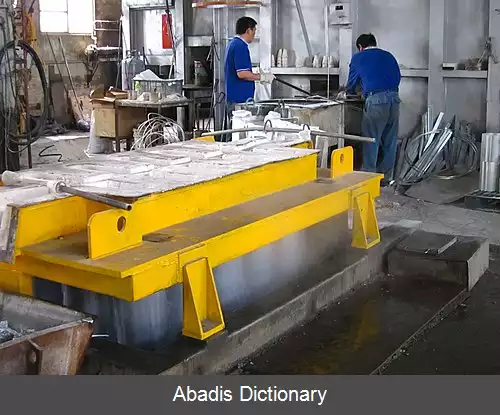
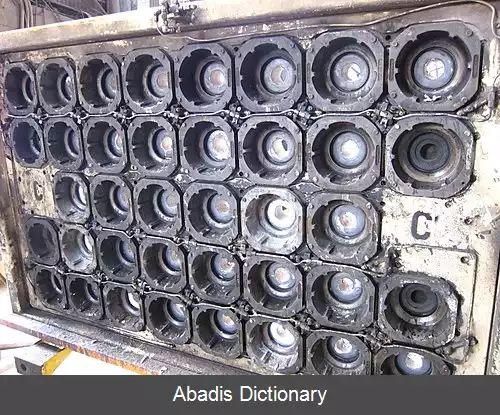
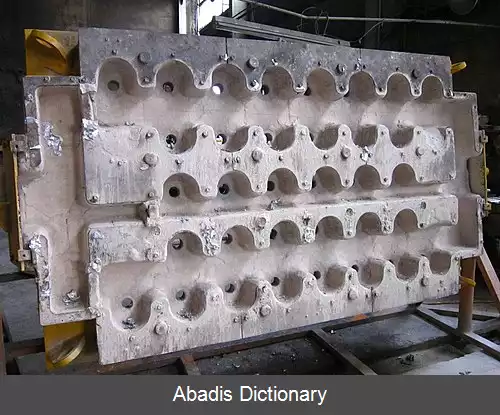
این نوشته برگرفته از سایت ویکی پدیا می باشد، اگر نادرست یا توهین آمیز است، لطفا گزارش دهید: گزارش تخلفدر سال ۱۹۵۰؛ برای تولید شمش، فولاد در قالب های ثابت ریخته می شد. از آن پس ریخته گری پیوسته در جهت افزایش کیفیت و کاهش هزینه های تولید پیشرفت های بسیاری کرد. این روش به دلیل داشتن هزینهٔ ذاتی کم و کیفیت بیشتر و همچنین داشتن کنترل در طول فرایند بسیار متداول است.
در واقع؛ شمش های آلومینیوم، برنج، مس، چدن و فولاد با مقطع مربعی، شش گوش و سایر مقطع تولید می شوند. مذاب با نیروی ثقل به داخل کریستالیزاتور هدایت می شود. شمش منجمد شده از مذاب، توسط سیستم کشنده به پایین کشیده می شود.
هنری بسمر، مشهور جهت فرایند بسمر، در سال ۱۸۵۷ حق امتیازی برای ریخته گری بین دو میلهٔ نورد دریافت کرد. اساس این فرایند، امروزه در ریخته گری نوار فولادی استفاده می شود.
فلز مذاب از طریق دهانه داخل کوره ریخته می شود. پس از انجام عملیات مربوط به دهانه؛ همچون ترکیب آلیاژی، گاز زدایی یا رساندن به دمای مناسب، تغذیه به قسمت بالایی دستگاه ریخته گری انتقال می یابد. معمولاً دهانه در محفظهٔ گردانی در بالای دستگاه ریخته گری قرار می گیرد. یکی از منابع تغذیه به صورت on - cast ( درحال تغذیهٔ دستگاه ریخته گری ) و منبع دیگر به حالت off - cast آماده می باشد و هنگامی که منبع تغذیه اولیه خالی شد، جایگزین آن می شود.
فلز داغ از منبع تغذیه توسط لولهٔ دیرگداز وارد حمام ثابتی به نام تاندیش می شود. تاندیش به مخزن فلز اجازه می دهد هنگام تغذیهٔ دستگاه ریخته گری، منبع های تغذیه جایگزین شوند. همچنین به عنوان یک حائل در برابر فلز داغ عمل کرده و به تدریج سیالیت فلز را کاهش می دهد. همین طور موجب تنظیم مقدار تغذیه لازم برای قالب ها و در نهایت تمیزکاری دستگاه می شود.
فلز توسط لولهٔ دیگری از تاندیش تخلیه شده و درون قالب باز مسی ریخته می شود. عمق قالب می تواند بین ۰٫۵ الی ۲ متر ( ۲۰ الی ۷۹ اینچ ) ، بسته به سرعت ریخته گری یا اندازهٔ قسمت، تغییر کند. سپس قالب آب سرد می شود تا فلز به طور مستقیم منجمد شود. این اولین مرحله از روش خنک کاری می باشد. همچنین به صورت عمودی ( و یا در یک راه منحنی عمودی ) نوسان می کند تا مانع چسبیدن فلز به دیواره های قالب شود. یک سیال روان کار ( و یا گاهی به صورت پودری که در برخورد با فلزات یا مایعات ذوب می شود ) اضافه می شود تا مانع چسبیدن و باقی ماندن ذرت در قالب شود – همچون ذرات اکسیدی - که امکان دارد روی فلز باشد و باعث شود روی مذاب جمع شود و یک لایه از ذرات و خاکستر را تشکیل دهد. لوله ای در قسمت پایین تعبیه شده است که مذاب نهفته در زیر لایهٔ ذرات را خارج می کند. به این لوله «نازل ورودی زیرآب» ( SEN ) گفته می شود. در برخی موارد لوله ها بین تاندیش و قالب استفاده نمی شوند. ( ریخته گری ریزش باز ) ؛ در این موارد نازل های قابل سنجش و تنظیم، که در قسمت انتهایی تاندیش قرار دارند، موجب هدایت فلز به داخل قالب می شوند. در برخی از طرح های ریخته گری پیوسته چندین قالب از یک تاندیش تغذیه می شوند.
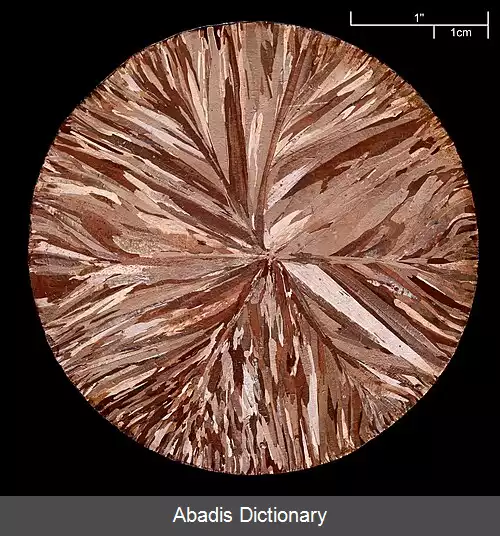
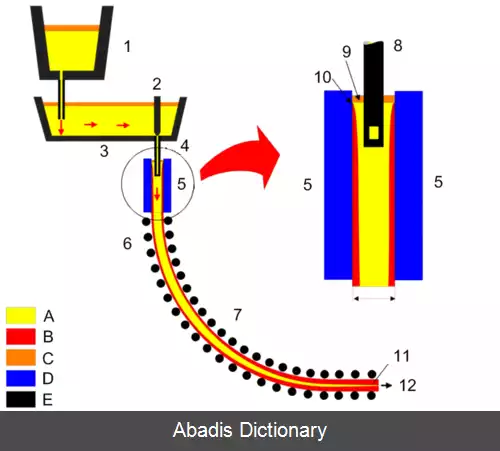
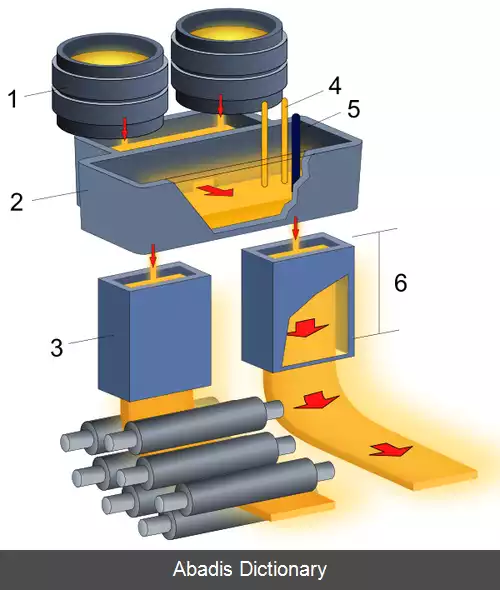
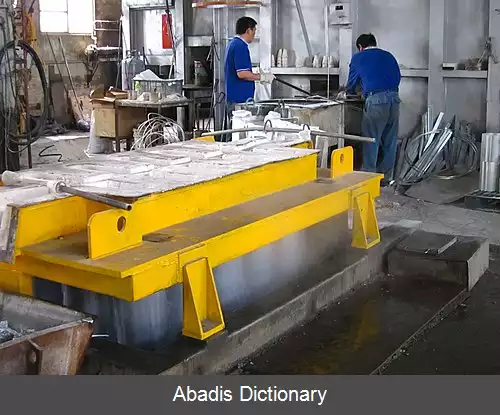
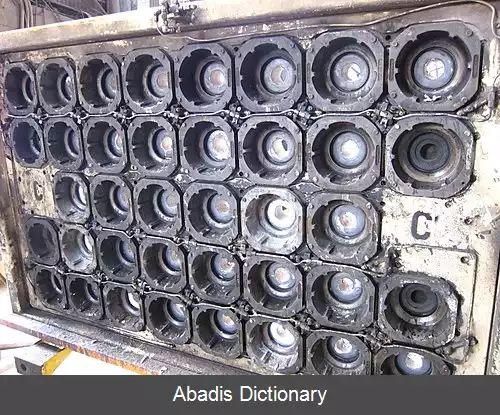
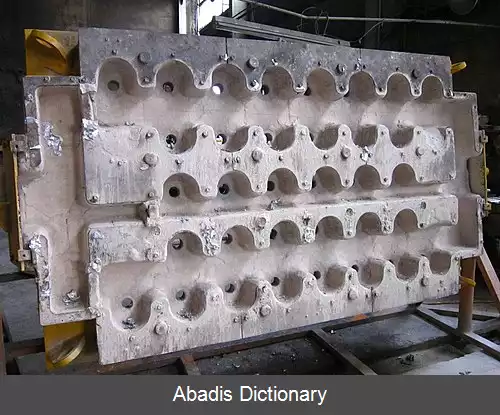
wiki: ریخته گری مداوم (پیوسته)