اسپینینگ ذوبی یک روش شکل دهی فلز است که به طور معمول برای ساخت لایه های نازک از فلز یا آلیاژهای با ساختار اتمی خاص استفاده می شود. [ ۱] برخی از کاربردهای مهم تجاری فلزات اسپینگ شده ذوبی، شامل ترانسفورماتورهای با بازده بالا ( ترانسفورماتور فلزی آمورف ) ، دستگاه های حسی، تجهیزات ارتباط از راه دور و الکترونیک قدرت است. یک فرایند اسپینینگ ذوبی متداول شامل ریخته گری فلز مذاب با هدایت پرفشار آن بر روی چرخ یا درام چرخشی است که داخل آن معمولاً توسط آب یا نیتروژن مایع خنک می شود.
مواد مذاب در اثر تماس با سطح سرد و بزرگ درام به سرعت منجمد می شوند. چرخش مداوم درام سبب بیرون اندازی محصول جامد شده می شود و سطح جدیدی را در معرض جریان فلز مذاب قرار می دهد و تولید پیوسته را امکان پذیر می کند. نوار حاصل سپس در امتداد خط تولید هدایت می شود تا بسته بندی یا به محصولات دیگر ماشین کاری شود. [ ۲] [ ۳] نرخ خنک سازی که با اسپینینگ ذوبی قابل دستیابی است، در محدوده ۱۰۴–۱۰۶ کلوین در ثانیه ( K / s ) است. در نتیجه، از اسپینینگ ذوبی برای توسعه موادی مانند شیشه های فلزی که به منظور شکل گیری به سرعت خنک کنندگی بسیار بالایی نیاز دارند، استفاده می شود. این محصولات به دلیل خنک سازی سریع، ساختار اتمی بسیار نامنظمی دارند که به آنها ویژگی های مغناطیسی و فیزیکی منحصر به فردی می بخشد ( به فلزات بی شکل مراجعه کنید ) . چندین تغییر در روند فرایند اسپینینگ ذوبی مزایای خاصی را ایجاد می کند. این فرایندها شامل ریخته گری جریان مسطح، اسپینینگ ذوبی با غلطک دوتایی، اسپینینگ ذوبی با بیرون اندازی خودکار است. با منشاگیری از تلاش های رابرت پاند در یک سری اختراعات ثبت شده مربوط به سالهای ۱۹۵۸–۱۹۶۱ ( شماره ثبت اختراعات ۲۸۲۵۱۰۸، ۲۹۱۰۷۴۴ و ۲۹۷۶۵۹۰ ایالات متحده ) ، مفهوم کنونی اسپینر مذاب توسط پاند و مادین در سال ۱۹۶۹ بیان شد، گرچه در ابتدا مایع در سطح داخلی درام منجمد می شد. لیبمن و گراهام در ادامه این روند را به عنوان یک روش ریخته گری پیوسته، این بار در سطح خارجی درام، توسعه دادند. [ ۴] این فرایند می تواند به طور مداوم نوارهای نازکی از مواد را تولید کند و ورق هایی با عرض چند اینچ به صورت تجاری در دسترس است.
در اسپینینگ ذوبی، آلیاژ یا فلز ابتدا در یک بوته ذوب می شود. سپس، از گاز بی اثر، معمولاً آرگون، به منظورهدایت پرفشار ماده مذاب به بیرون نازل استفاده می شود. جریان حاصل مایع به سطح محیط خارجی چرخ یا درام چرخشی هدایت می شود که به طور داخلی خنک می شود. سطح خارجی درام بسیار نزدیک به نازل قرار دارد، اما آن را لمس نمی کند. به طور کلی، سرعت سطح درام باید بین ۱۰ تا ۶۰ متر بر ثانیه باشد تا به ترتیب از تشکیل قطرات یا شکستن لایه ها جلوگیری شود. هنگامی که جریان مذاب با سطح درام تماس می یابد، یک گودال کوچک ذوب ( مواد مذاب ) تشکیل می شود. به دلیل گرانروی کم مذاب، نیروهای برشی تولید شده توسط حرکت نسبی سطح درام در زیر مذاب فقط چند میکرون به داخل گودال گسترش می یابد. به عبارت دیگر، فقط مقدار کمی از گودال تحت تأثیر اصطکاک ناشی از چرخش درام است. در نتیجه، هنگامی که درام می چرخد، بیشتر گودال ذوب شده توسط کشش سطح بین نازل و درام حفظ می شود. با این حال، مذاب در ته گودال، که در تماس مستقیم با درام است، به سرعت به یک نوار نازک منجمد می شود. لایه منجمد شده تا ۱۰ درجه چرخش از زیر نازل و سطح درام دور می شود. قبل از اینکه نیروی گریز از مرکز از چرخش درام آن را بیرون بکشد. [ ۱] [ ۳] [ ۵] این فرایند به طور پیوسته اتفاق می افتد، بنابراین با خارج شدن مواد جامد از زیر گودال مذاب، مواد مذاب بیشتری از نازل به گودال اضافه می شود.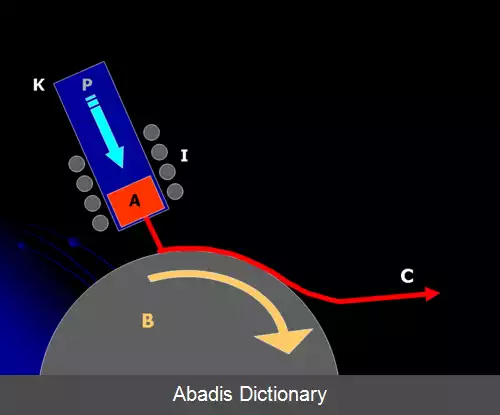
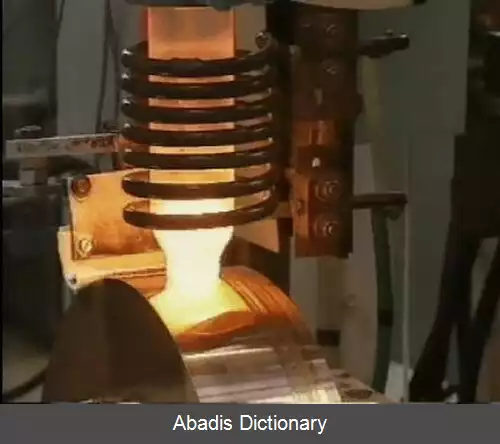
این نوشته برگرفته از سایت ویکی پدیا می باشد، اگر نادرست یا توهین آمیز است، لطفا گزارش دهید: گزارش تخلفمواد مذاب در اثر تماس با سطح سرد و بزرگ درام به سرعت منجمد می شوند. چرخش مداوم درام سبب بیرون اندازی محصول جامد شده می شود و سطح جدیدی را در معرض جریان فلز مذاب قرار می دهد و تولید پیوسته را امکان پذیر می کند. نوار حاصل سپس در امتداد خط تولید هدایت می شود تا بسته بندی یا به محصولات دیگر ماشین کاری شود. [ ۲] [ ۳] نرخ خنک سازی که با اسپینینگ ذوبی قابل دستیابی است، در محدوده ۱۰۴–۱۰۶ کلوین در ثانیه ( K / s ) است. در نتیجه، از اسپینینگ ذوبی برای توسعه موادی مانند شیشه های فلزی که به منظور شکل گیری به سرعت خنک کنندگی بسیار بالایی نیاز دارند، استفاده می شود. این محصولات به دلیل خنک سازی سریع، ساختار اتمی بسیار نامنظمی دارند که به آنها ویژگی های مغناطیسی و فیزیکی منحصر به فردی می بخشد ( به فلزات بی شکل مراجعه کنید ) . چندین تغییر در روند فرایند اسپینینگ ذوبی مزایای خاصی را ایجاد می کند. این فرایندها شامل ریخته گری جریان مسطح، اسپینینگ ذوبی با غلطک دوتایی، اسپینینگ ذوبی با بیرون اندازی خودکار است. با منشاگیری از تلاش های رابرت پاند در یک سری اختراعات ثبت شده مربوط به سالهای ۱۹۵۸–۱۹۶۱ ( شماره ثبت اختراعات ۲۸۲۵۱۰۸، ۲۹۱۰۷۴۴ و ۲۹۷۶۵۹۰ ایالات متحده ) ، مفهوم کنونی اسپینر مذاب توسط پاند و مادین در سال ۱۹۶۹ بیان شد، گرچه در ابتدا مایع در سطح داخلی درام منجمد می شد. لیبمن و گراهام در ادامه این روند را به عنوان یک روش ریخته گری پیوسته، این بار در سطح خارجی درام، توسعه دادند. [ ۴] این فرایند می تواند به طور مداوم نوارهای نازکی از مواد را تولید کند و ورق هایی با عرض چند اینچ به صورت تجاری در دسترس است.
در اسپینینگ ذوبی، آلیاژ یا فلز ابتدا در یک بوته ذوب می شود. سپس، از گاز بی اثر، معمولاً آرگون، به منظورهدایت پرفشار ماده مذاب به بیرون نازل استفاده می شود. جریان حاصل مایع به سطح محیط خارجی چرخ یا درام چرخشی هدایت می شود که به طور داخلی خنک می شود. سطح خارجی درام بسیار نزدیک به نازل قرار دارد، اما آن را لمس نمی کند. به طور کلی، سرعت سطح درام باید بین ۱۰ تا ۶۰ متر بر ثانیه باشد تا به ترتیب از تشکیل قطرات یا شکستن لایه ها جلوگیری شود. هنگامی که جریان مذاب با سطح درام تماس می یابد، یک گودال کوچک ذوب ( مواد مذاب ) تشکیل می شود. به دلیل گرانروی کم مذاب، نیروهای برشی تولید شده توسط حرکت نسبی سطح درام در زیر مذاب فقط چند میکرون به داخل گودال گسترش می یابد. به عبارت دیگر، فقط مقدار کمی از گودال تحت تأثیر اصطکاک ناشی از چرخش درام است. در نتیجه، هنگامی که درام می چرخد، بیشتر گودال ذوب شده توسط کشش سطح بین نازل و درام حفظ می شود. با این حال، مذاب در ته گودال، که در تماس مستقیم با درام است، به سرعت به یک نوار نازک منجمد می شود. لایه منجمد شده تا ۱۰ درجه چرخش از زیر نازل و سطح درام دور می شود. قبل از اینکه نیروی گریز از مرکز از چرخش درام آن را بیرون بکشد. [ ۱] [ ۳] [ ۵] این فرایند به طور پیوسته اتفاق می افتد، بنابراین با خارج شدن مواد جامد از زیر گودال مذاب، مواد مذاب بیشتری از نازل به گودال اضافه می شود.
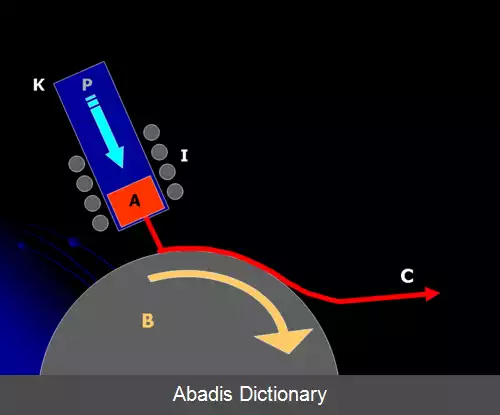
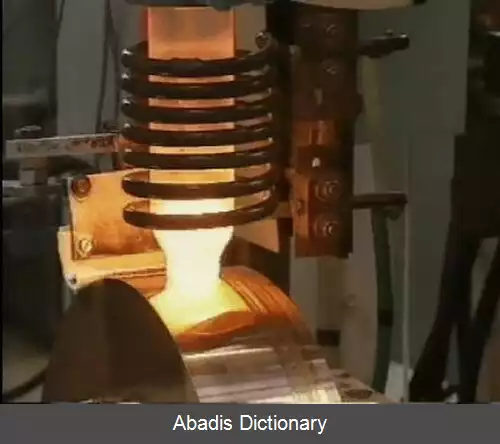
wiki: شکل دهی ذوبی