شکل دهی برشی ( به انگلیسی: shear forming ) که به آن چرخش برشی نیز گفته می شود، مشابه شکل دهی چرخشی فلزات ( به انگلیسی: shear spinning ) است. در چرخش برشی، مساحت قطعه نهایی تقریباً مساوی با ورق فلز مسطح است. ضخامت دیواره با فاصله بین غلتک و سنبه کنترل می شود. در شکل دهی برشی، در دیواره کاهش ضخامت اتفاق می افتد.
تا پیش از دهه ۱۹۵۰، عملیات چرخش به وسیله یک ماشین تراش ساده انجام می شد. هنگامی که فن آوری های جدیدی به حوزه شکل دهی فلزات وارد شدند و دستگاه های چرخشی اختصاصی با قدرت در دسترس بودند، توسعه شکل دهی برشی در سوئد آغاز شد.
شکل ۲ شماتیک یک فرایند شکل دهی برشی را نشان می دهد.
• یک ورق فلز بین سنبه و چاک دستگاه چرخش قرار می گیرد. سنبه شکل داخلی قطعه مورد نظر نهایی را دارد.
• یک غلتک باعث می شود ورق فلز به دور سنبه پیچیده شود تا شکل مورد نظر را به خود بگیرد.
همان طور که در شکل قابل مشاهده است، s1 که ضخامت ابتدایی دیواره قطعه کار است، به s0 کاهش می یابد.
در شکل دهی برشی، قطعه کار اولیه می تواند مقطع دایره ای یا مستطیلی داشته باشد. از طرف دیگر، شکل پروفیل قطعه نهایی می تواند مقعر، محدب یا ترکیبی از این دو باشد.
ماشین شکل دهی برشی بسیار شبیه ماشین چرخش معمولی است، با این تفاوت که باید در برابر نیروها مقاومت بسیار بیشتری داشته باشد، زیرا نیروهایی که برای انجام عملیات برش لازم هستند بسیار بالاتر هستند.
طراحی غلتک باید با دقت انجام شود، زیرا بر روی شکل قطعه، ضخامت دیواره و دقت ابعادی تأثیر می گذارد. هرچه شعاع دماغه ابزار کمتر باشد، تنش ها بیشتر می شوند و کمترین میزان یکنواختی در ضخامت حاصل می شود.
قابلیت چرخش، که بعضی اوقات با عنوان قابلیت چرخش برشی هم شناخته می شود، می تواند به عنوان توانایی یک فلز برای قرار گرفتن تحت تغییر شکل چرخش برشی بدون افزایش مقاومت کششی و پارگی تعریف شود. در مورد قابلیت چرخش، از دو نویسنده، کگ و کالپاکچوگلو، یک کار منتشر شده و در دسترس است.
کگ پیش بینی کرد که برای ماده ای با کاهش کشش ۸۰٪، کاهش چرخش نهایی برابر یا بیشتر از ۸۰٪ باشد. کالپاکچوگلو نتیجه گرفت که برای فلزات با کرنش شکست واقعی ۰٫۵ یا بیشتر، برای کاهش شکل دهی برشی یک حداکثر حد وجود دارد. برای مواد با کرنش واقعی کمتر از ۰٫۵، قابلیت چرخش به شکل پذیری مواد بستگی دارد. [ ۱] [ ۲]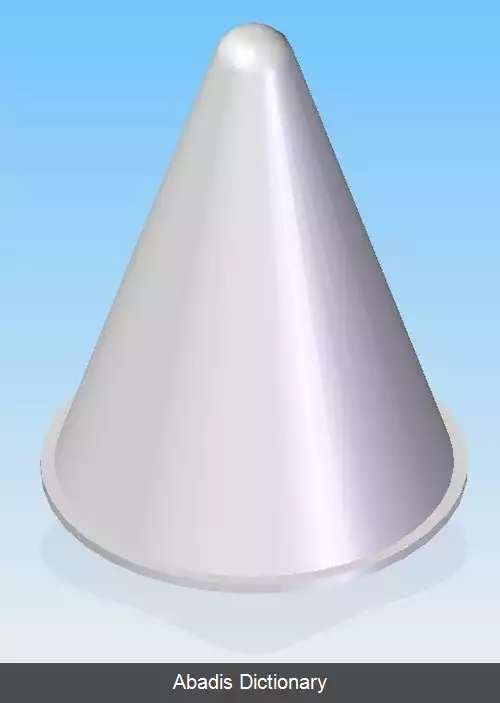
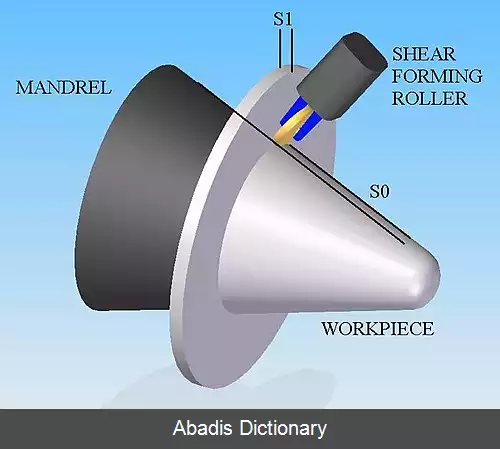
این نوشته برگرفته از سایت ویکی پدیا می باشد، اگر نادرست یا توهین آمیز است، لطفا گزارش دهید: گزارش تخلفتا پیش از دهه ۱۹۵۰، عملیات چرخش به وسیله یک ماشین تراش ساده انجام می شد. هنگامی که فن آوری های جدیدی به حوزه شکل دهی فلزات وارد شدند و دستگاه های چرخشی اختصاصی با قدرت در دسترس بودند، توسعه شکل دهی برشی در سوئد آغاز شد.
شکل ۲ شماتیک یک فرایند شکل دهی برشی را نشان می دهد.
• یک ورق فلز بین سنبه و چاک دستگاه چرخش قرار می گیرد. سنبه شکل داخلی قطعه مورد نظر نهایی را دارد.
• یک غلتک باعث می شود ورق فلز به دور سنبه پیچیده شود تا شکل مورد نظر را به خود بگیرد.
همان طور که در شکل قابل مشاهده است، s1 که ضخامت ابتدایی دیواره قطعه کار است، به s0 کاهش می یابد.
در شکل دهی برشی، قطعه کار اولیه می تواند مقطع دایره ای یا مستطیلی داشته باشد. از طرف دیگر، شکل پروفیل قطعه نهایی می تواند مقعر، محدب یا ترکیبی از این دو باشد.
ماشین شکل دهی برشی بسیار شبیه ماشین چرخش معمولی است، با این تفاوت که باید در برابر نیروها مقاومت بسیار بیشتری داشته باشد، زیرا نیروهایی که برای انجام عملیات برش لازم هستند بسیار بالاتر هستند.
طراحی غلتک باید با دقت انجام شود، زیرا بر روی شکل قطعه، ضخامت دیواره و دقت ابعادی تأثیر می گذارد. هرچه شعاع دماغه ابزار کمتر باشد، تنش ها بیشتر می شوند و کمترین میزان یکنواختی در ضخامت حاصل می شود.
قابلیت چرخش، که بعضی اوقات با عنوان قابلیت چرخش برشی هم شناخته می شود، می تواند به عنوان توانایی یک فلز برای قرار گرفتن تحت تغییر شکل چرخش برشی بدون افزایش مقاومت کششی و پارگی تعریف شود. در مورد قابلیت چرخش، از دو نویسنده، کگ و کالپاکچوگلو، یک کار منتشر شده و در دسترس است.
کگ پیش بینی کرد که برای ماده ای با کاهش کشش ۸۰٪، کاهش چرخش نهایی برابر یا بیشتر از ۸۰٪ باشد. کالپاکچوگلو نتیجه گرفت که برای فلزات با کرنش شکست واقعی ۰٫۵ یا بیشتر، برای کاهش شکل دهی برشی یک حداکثر حد وجود دارد. برای مواد با کرنش واقعی کمتر از ۰٫۵، قابلیت چرخش به شکل پذیری مواد بستگی دارد. [ ۱] [ ۲]
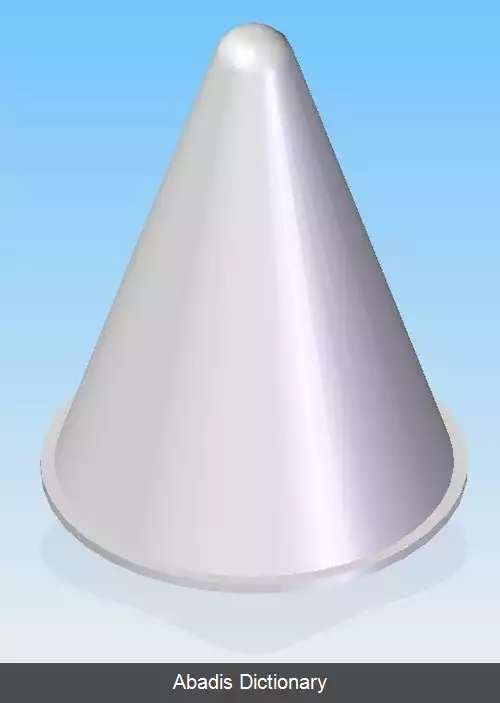
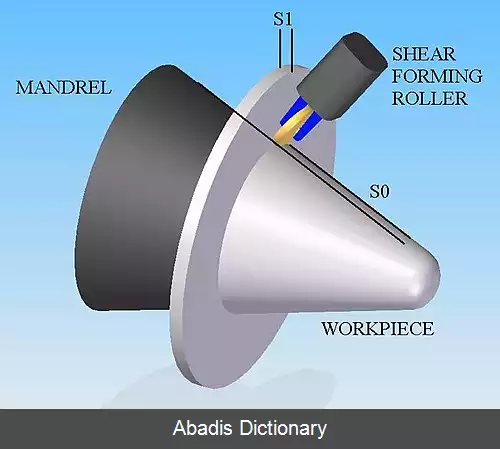
wiki: شکل دهی برشی