فرایند جوشکاری اصطکاکی اغتشاشی ( به انگلیسی: Friction Stir Welding ) در سال ۱۹۹۱ توسط موسسه جوشکاری انگلستان و با همکاری دانشگاه کمبریج، به عنوان یک روش اتصال حالت جامد اختراع شد و برای اولین بار برای جوشکاری آلیاژهای آلومینیوم به کار برده شد[ ۱] . جوشکاری اصطکاکی اغتشاشی به عنوان مهم ترین پیشرفت در اتصال فلزات در دهه آخر قرن بیستم به حساب می آید و با توجه به انرژی مصرفی کم و عدم ایجاد آلودگی به عنوان یک فناوری سبز محسوب می شود[ ۲] . در این فرایند از گاز یا پوشش محافظ برای حفاظت از حوضچه مذاب استفاده نمی شود و همین مسئله موجب می شود این فرایند در دسته فرایندهای دوستدار محیط زیست قرار گیرد. این فرایند در دسته فرایندهای جوشکاری حالت جامد قرار می گیرد و از این فرایند برای اتصال دهی موادی که با فرایندهای متداول جوشکاری قابلیت جوش پذیری ندارند، استفاده می شود[ ۳] [ ۴] [ ۵] .
لازم به ذکر است از این فرآیند برای جوشکاری مواد پلیمری ( که از طریق جوشکاری های مرسوم مانند جوش قوس الکتریکی و غیره که امکان اتصال وجود ندارد. ) نیز استفاده می گردد . همچنین جوشکاری مواد کامپوزیتی پایه پلمیری و نانو مواد مانند نانو تیوب های کربنی و. . . نیز با این فرآیند در حال بررسی و تحقیق میباشد.
فرایند جوشکاری اصطکاکی اغتشاشی یک نوع فرایند جوشکاری حالت جامد می باشد که در آن اتصال به وسیله دوران یک ابزار غیر قابل مصرف انجام میگیرد. موادی که به وسیله این فرایند قابل اتصال هستند شامل: آلومینیوم، سرب، منیزیم، فولاد، تیتانیم، روی، مس و مواد کامپوزیتی هستند. اتصال بسیاری از آلیاژها که با استفاده از روش های ذوبی سخت یا غیر ممکن است با استفاده از این روش بسیار راحت صورت می گیرد[ ۶] . مراحل انجام فرایند به این صورت است که ابتدا یک ابزار با هندسه مشخص متشکل از شانه و پین که در حال دوران است، وارد درز اتصال می شود. در اثر اصطکاک ناشی از دوران ابزار درون مواد، حرارت و تغییر شکل پلاستیک ایجاد می گردد. زمانی که ابزار تا عمق مشخصی ( طوری که معمولاً شانه مماس بر سطح باشد ) درون مواد فرورفت، آنگاه تقریباً بعد از ۶۰ ثانیه ابزار شروع به حرکت انتقالی می نماید. حرکت انتقالی ابزار و همچنین حرارت ناشی از اصطکاک باعث پر شدن درز اتصال میشود. ناحیه ی اثر ابزار که در حین جوشکاری در پشت ابزار به صورت نواری روی سطح قطعات باقی می ماند، ردپای شانه ی ابزار نامیده می شود. به سمتی که سرعت زاویه ای ابزار هم جهت با سرعت جوشکاری است، سمت پیش رونده و به سمتی از اتصال که این دو سرعت در خلاف جهت یکدیگر باشند، سمت پس رونده گفته می شود. در واقع دو سمت یک اتصال با هم از نظر تجربه ی پدیده های ترمومکانیکی متفاوتند و در همه جا در بررسی عرضی فرایند جوشکاری اصطکاکی اغتشاشی از سطح مقطع این نوع جوش ها باید نواحی یادشده مشخص گردد.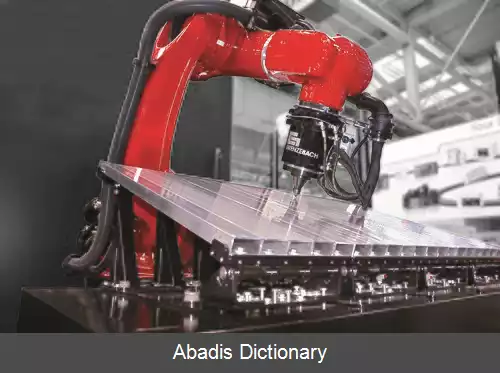
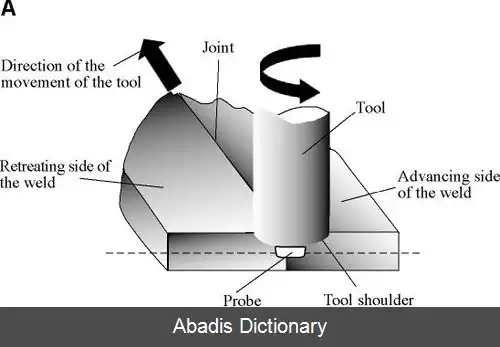
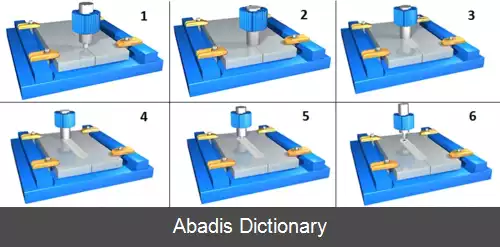
این نوشته برگرفته از سایت ویکی پدیا می باشد، اگر نادرست یا توهین آمیز است، لطفا گزارش دهید: گزارش تخلفلازم به ذکر است از این فرآیند برای جوشکاری مواد پلیمری ( که از طریق جوشکاری های مرسوم مانند جوش قوس الکتریکی و غیره که امکان اتصال وجود ندارد. ) نیز استفاده می گردد . همچنین جوشکاری مواد کامپوزیتی پایه پلمیری و نانو مواد مانند نانو تیوب های کربنی و. . . نیز با این فرآیند در حال بررسی و تحقیق میباشد.
فرایند جوشکاری اصطکاکی اغتشاشی یک نوع فرایند جوشکاری حالت جامد می باشد که در آن اتصال به وسیله دوران یک ابزار غیر قابل مصرف انجام میگیرد. موادی که به وسیله این فرایند قابل اتصال هستند شامل: آلومینیوم، سرب، منیزیم، فولاد، تیتانیم، روی، مس و مواد کامپوزیتی هستند. اتصال بسیاری از آلیاژها که با استفاده از روش های ذوبی سخت یا غیر ممکن است با استفاده از این روش بسیار راحت صورت می گیرد[ ۶] . مراحل انجام فرایند به این صورت است که ابتدا یک ابزار با هندسه مشخص متشکل از شانه و پین که در حال دوران است، وارد درز اتصال می شود. در اثر اصطکاک ناشی از دوران ابزار درون مواد، حرارت و تغییر شکل پلاستیک ایجاد می گردد. زمانی که ابزار تا عمق مشخصی ( طوری که معمولاً شانه مماس بر سطح باشد ) درون مواد فرورفت، آنگاه تقریباً بعد از ۶۰ ثانیه ابزار شروع به حرکت انتقالی می نماید. حرکت انتقالی ابزار و همچنین حرارت ناشی از اصطکاک باعث پر شدن درز اتصال میشود. ناحیه ی اثر ابزار که در حین جوشکاری در پشت ابزار به صورت نواری روی سطح قطعات باقی می ماند، ردپای شانه ی ابزار نامیده می شود. به سمتی که سرعت زاویه ای ابزار هم جهت با سرعت جوشکاری است، سمت پیش رونده و به سمتی از اتصال که این دو سرعت در خلاف جهت یکدیگر باشند، سمت پس رونده گفته می شود. در واقع دو سمت یک اتصال با هم از نظر تجربه ی پدیده های ترمومکانیکی متفاوتند و در همه جا در بررسی عرضی فرایند جوشکاری اصطکاکی اغتشاشی از سطح مقطع این نوع جوش ها باید نواحی یادشده مشخص گردد.
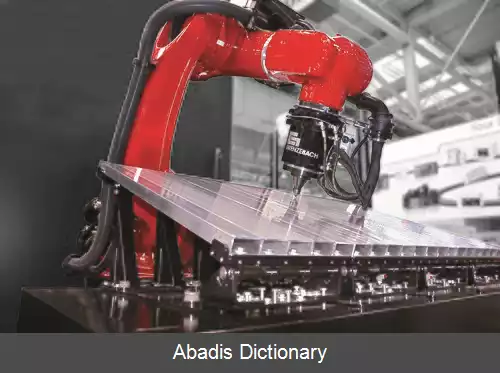
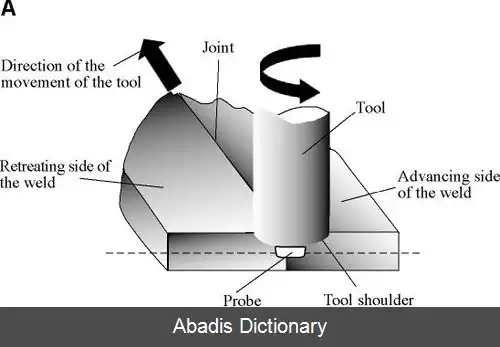
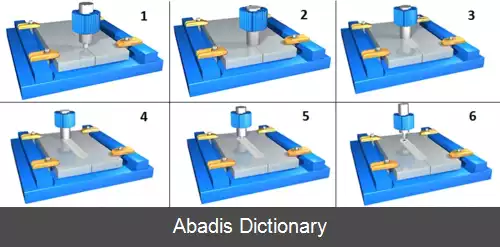